National Group rolls out two new generation Cat D11 Dozers, including the worlds first
As seen in Australian Mining Magazine – March 2020 Edition, written by Salomae Haselgrove.
The National Group prides itself on offering Australian mining the best and most innovative machinery. The new Cat D11 dozer, the latest piece in this extensive range, is no exception. Salomae Haselgrove writes.
The Cat D11 dozer is an exciting addition to the National Group’s fleet, featuring new technology such as load sensing hydraulics and a fuel remap, while maintaining the classic features customers know and love about this series of machine.
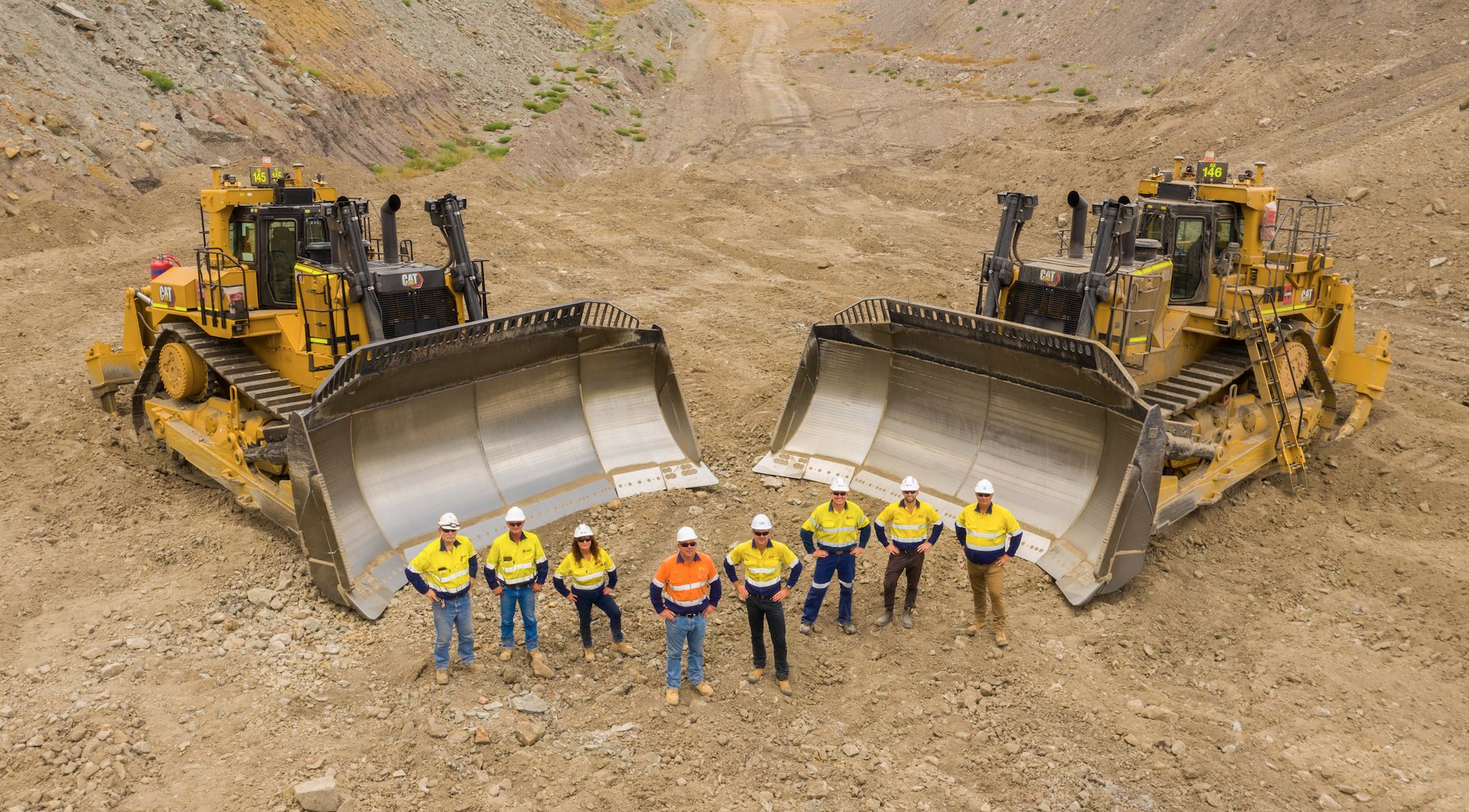
Queensland-based Caterpillar dealer Hastings Deering, which has delivered the D11 to Australia alongside National Group, has described the dozers as “keeping everything customers liked about the previous model, but just making it better”.
Caterpillar has designed the Cat D11 to move more material efficiently and safely at a faster cycle time to produce more dirt at a lower cost per tonne.
The Cat D11 boasts new load-sensing flexible hydraulics and high horsepower reverse to deliver up to 8 per cent fuel efficiency improvement on past models.
Its hydraulic pumps are adjustable, allowing operators to adjust the output to meet demand, which helps mine sites save energy, reduce heat generation and extend machine life.
National Group has secured the world’s first model of the innovative new dozers straight off the production line and endorses the dozer’s smart new design.
The company has wasted no time putting the Cat D11 dozer to work, with it hitting the dirt at BHP Mitsubishi Alliance’s (BMA) Blackwater mine in Queensland in December last year, and another deployed in January of this year.
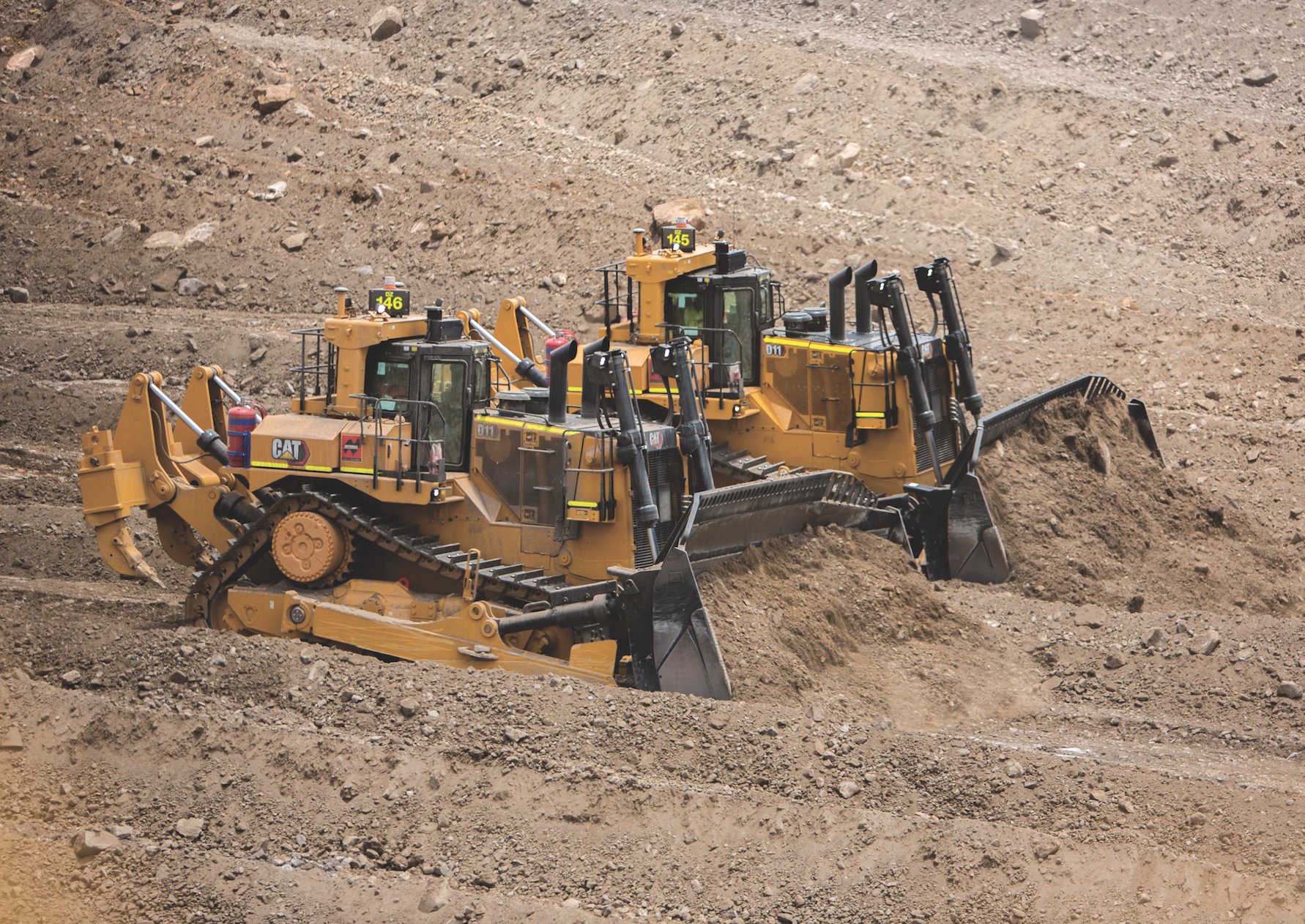
National Group is so impressed with the latest model of the dozer it has ordered four additional machines, which are set to arrive over the coming months.
“Our team prides ourselves on having the best equipment available for our clients,” National Group Managing Director Mark Ackroyd says.
“Securing the first ever Cat D11 dozer in the world is testament to this. The D11 is the industry’s best large dozer, so it was a logical choice for us to bring in six new dozers to our expansive fleet.”
Ackroyd is also making the new dozers unique to the company, with all six of the machines to be fitted with a reclamation blade.
This is also known as an XU blade, which extends the dozer from a 34-cubic-metre blade to a 42.2-cubic-metre blade for maximum reach.
The reclamation blades are more productive than the U blade on previous models; they reduce cost per tonne, while still handling the harsh conditions of a mine site as its predecessor did.
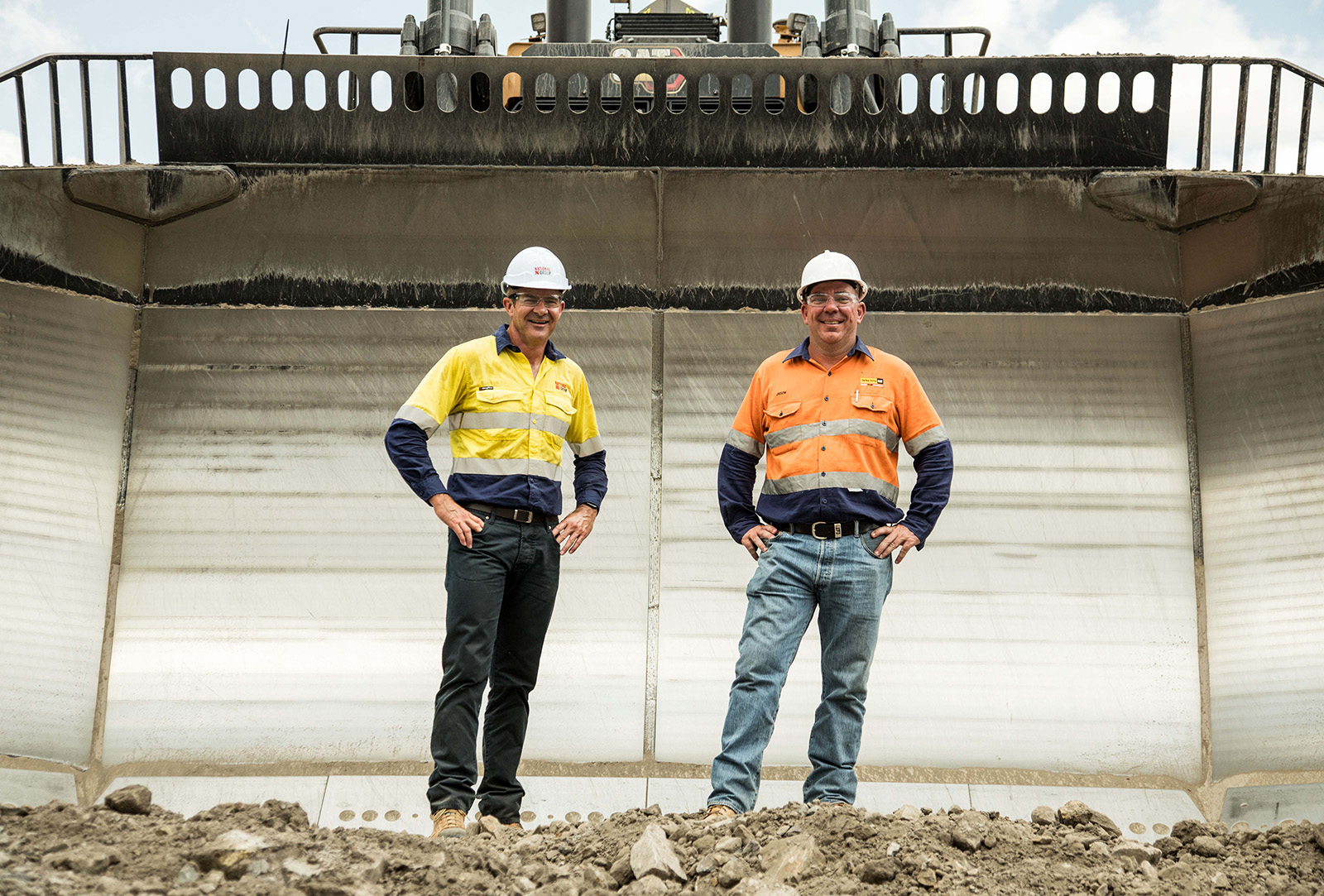
Left: Mark Ackroyd, National Group Managing Director. Right: Jason Garea, Hastings Deering Mining Account Manager.
The Cat D11 dozer has a new case and frame design, which improves its bearings. This, plus redesigned pin joints and a 30 per cent larger oil pan, lowers maintenance and repair costs, according to Mark Ackroyd.
“We expect a lower maintenance and repair cost of up to 5 per cent thanks to the new case and frame design,” he says.
Expanding on Cat’s existing safety features, the D11 boasts improved safety on previous models, with the engine oil sump capacity made 30 per cent larger, which extends the preventative maintenance intervals to 500 hours, giving operators less maintenance downtime.
The electrical centre is based on ground-level, which provides convenient and safe access to the lockout control, engine shutdown switch and ladder raise and lower switches.
For more efficient and safe maintenance, the Cat D11 dozer hosts an Auto Lube system, which means service technicians can change the coolant, hydraulic, engine and powertrain oil from ground level.
There are also optional add on safety features, including sealed or partial bottom guards, undercarriage idler guards and grill door screens, further guaranteeing operator safety.
Caterpillar has also taken advantage of advancing technology, incorporating automated blade assist into the D11 dozer, which increases efficiency while reducing the workload on operators.
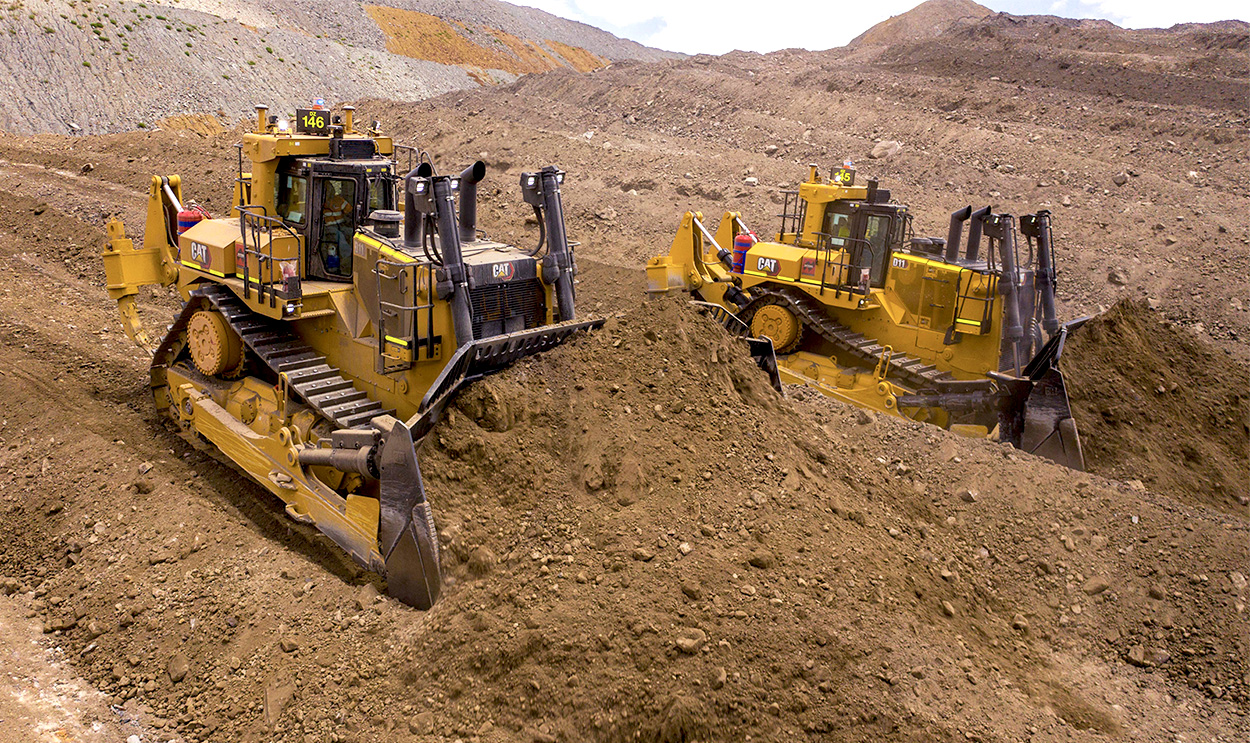
This is in addition to AutoCarry, which operators can activate to automatically change blade positions to keep track while pushing a load and avoid accidents caused by operator fatigue.
There is also the option to add extras for comfort, such as air conditioning, heated and ventilated seats and window shades, for a comfortable day at work regardless of the outside conditions.
National Group’s Blackwater Project Manager Scott Millane says the dozers are already immensely popular within the sector, due to their improved design for safety purposes.
“The other thing that makes them fight over these dozers is the increased torque.
“If there’s an area that’s had some mud stone ripped up, the operators can put the rippers all the way down and the dozer just pulls through.”
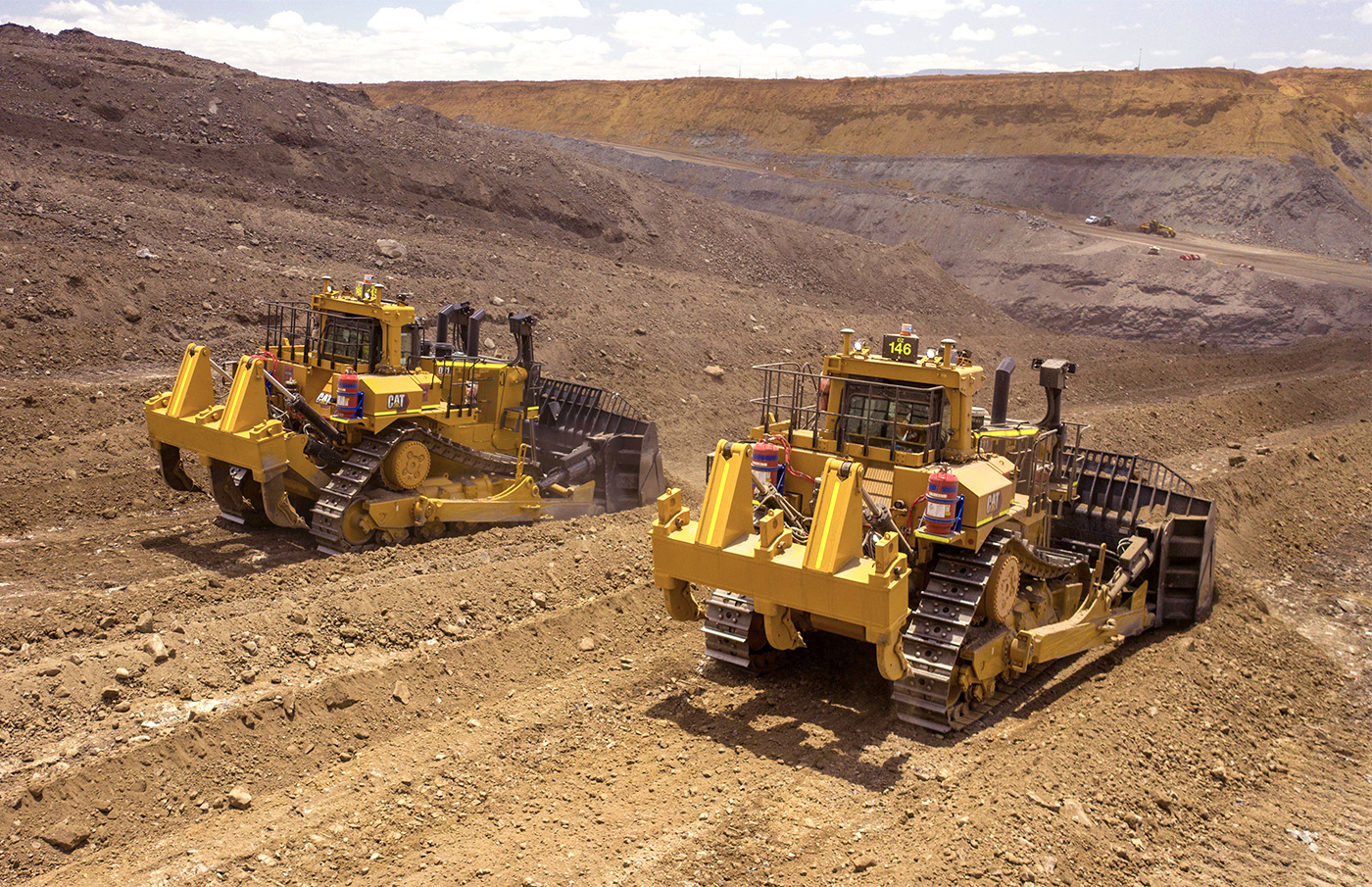
Hastings Deering mining account manager Jason Garea spoke about their relationship with National Group and how much it has grown from strength to strength over many projects.
“We have had a long-standing relationship with National Group and being able to deliver another world first with the D11 is a demonstration of things to come,” Garea says.
“Mark is committed to innovation and technology. The D11 Dozer has integrated technologies built into it, including terrain which makes for more accuracy on job sites which will ultimately reduce rework.”
The partnership will continue to monitor how the D11s perform in Australia as the remainder of the six machines are rolled across mine sites this year.