Global trends in mining equipment and transport logistics
Mining equipment is one of the world’s largest industries valued in 2019 at US$144.37 billion. Research by Grand View predicts significant growth at a compound annual growth rate (CAGR) of 12.7% from 2020 to 2027 for mining equipment such as excavators, trucks and dozers. Grand View also identified a paradigm shift from traditional underground mining to open-pit mining, with advancements in technologies and autonomous equipment expected to play a larger role in the mining industry of the future.
Hitachi Construction Machinery recently announced their intention to trial autonomous, heavy earthmoving hydraulic excavators in Australia. Trials are expected to commence in April 2021 according to a Hitachi spokesperson, with safety and increased mine site productivity being a key benefit. Hitachi excavators will be equipped with operator support systems such as a collision-avoidance system with other mining equipment in order to improve mine site safety.
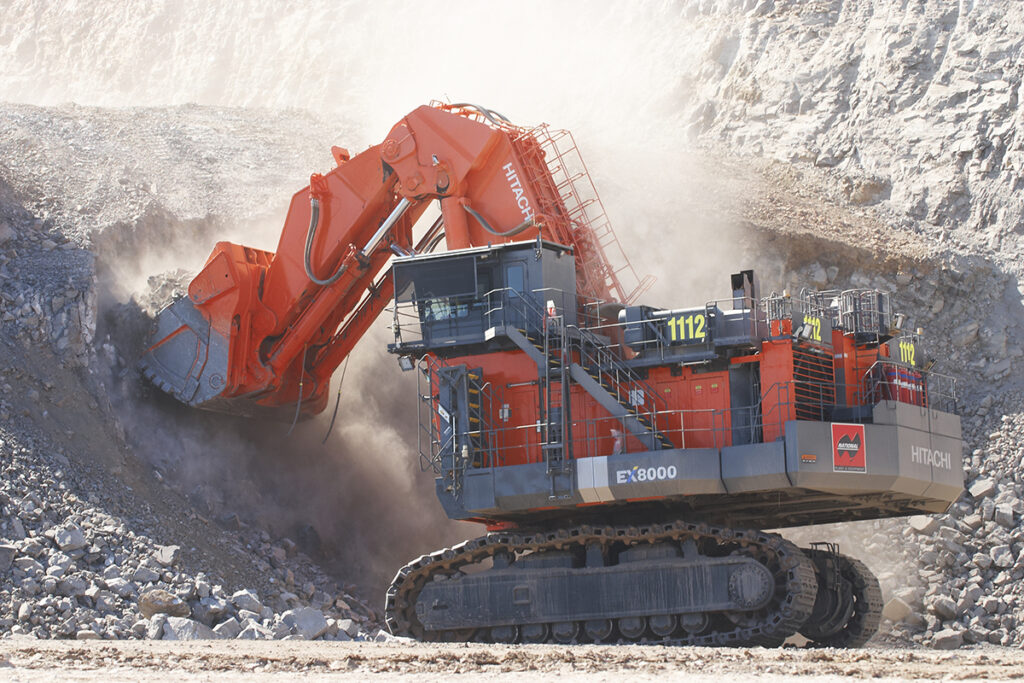
Wolff Mining, part of the National Group are well-known in the Australian mining industry for their implementation and optimisation of semi-autonomous tractor system (SATS) technology. In association with Caterpillar on their Cat Command for Dozing module, Wolff Mining’s technology is a world’s-first application into a mining production environment, providing the ability for one operator to control up to four dozers from a control room.
Mark Ackroyd, National Group Managing Director suggests that “the mining industry faces challenges, some that autonomous equipment will solve. Wolff Mining’s autonomous dozer push for instance continues to increase safety, productivity and mine site efficiency. It has also enabled mine sites to continue to operate whilst some operations elsewhere have ceased due to the current situation. Another key factor that will always have a significant impact on the mining industry as a whole is the value of commodities, which can impact mining companies all the way down to an operational level.”
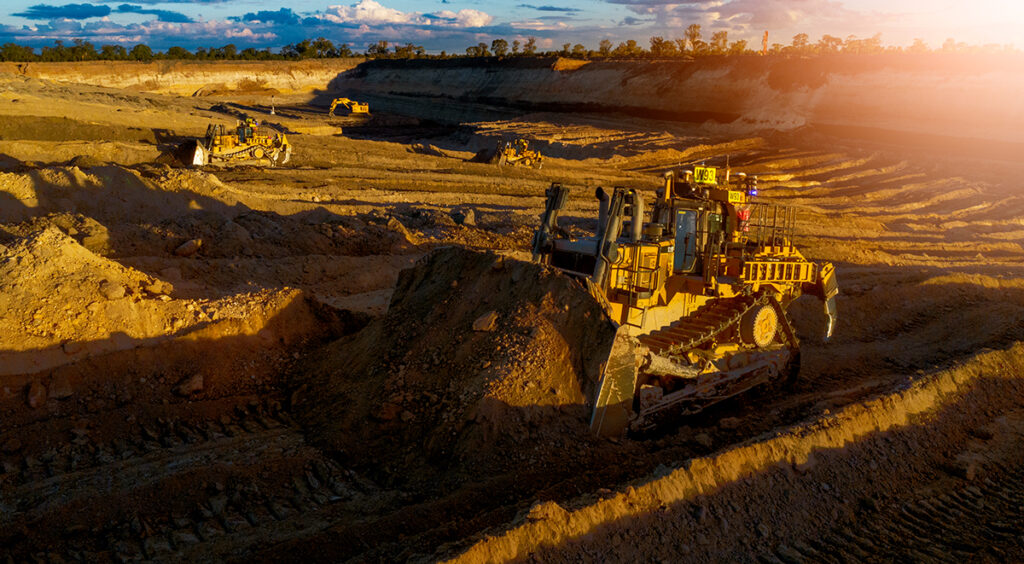
“If the value of a particular commodity is high, this is an attractive prospect for mining companies and will encourage them to increase their volume of mining for that particular resource, at that particular time. We have seen the price of iron ore skyrocket during the COVID-19 pandemic, in which companies such as Fortescue Metals Group (FMG) have benefitted from. Gold is another stand out, which recently reached over US$2,000 per ounce. Mining companies such as Evolution Mining are well placed at the moment due to the high price of Gold. But due to the volatility of commodity prices and other known or unknown global factors, the future is not always certain.”
“National Plant & Equipment, part of the National Group specialises in the dry hire of heavy mining equipment, a model that many companies are adopting versus buying their own equipment. Following a renting model can help mining companies free up capital expenditure, in order to keep something in reserve to pursue other more attractive ventures. Due to this fact, many mining companies are actually choosing to dispose of their mining equipment and rent instead.”
“National Machinery Xchange, part of the National Group caters for the growing need for mining companies to dispose of mining equipment in order to raise capital and reduce costs through leasing versus buying equipment” notes Ackroyd.
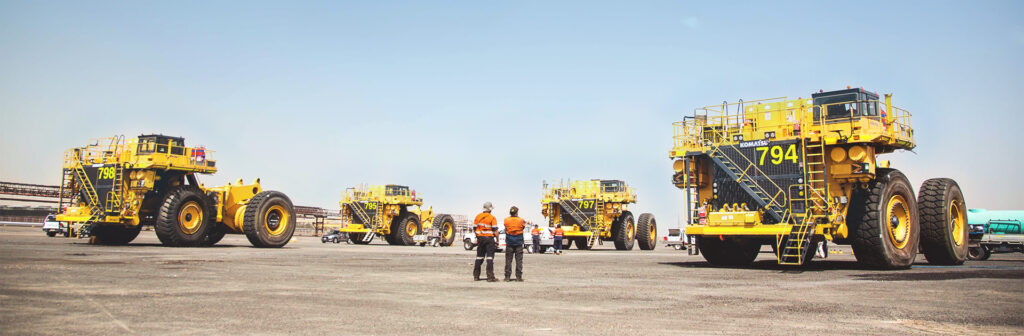
But with all this being said, whether you rent or buy mining equipment, there is another problem that requires a solution. How do you get some of the largest machines of the planet, from one side of the globe to the other, effectively and without incident, time after time?
The Liebherr 9800 Excavator for instance can take up to 18 months to manufacture and can weigh an astonishing 800 tons. Equipment of this size is unable to be transported in one piece due to the sheer size and the nature of the logistics involved. It is therefore transported in parts and assembled on site at its final destination.
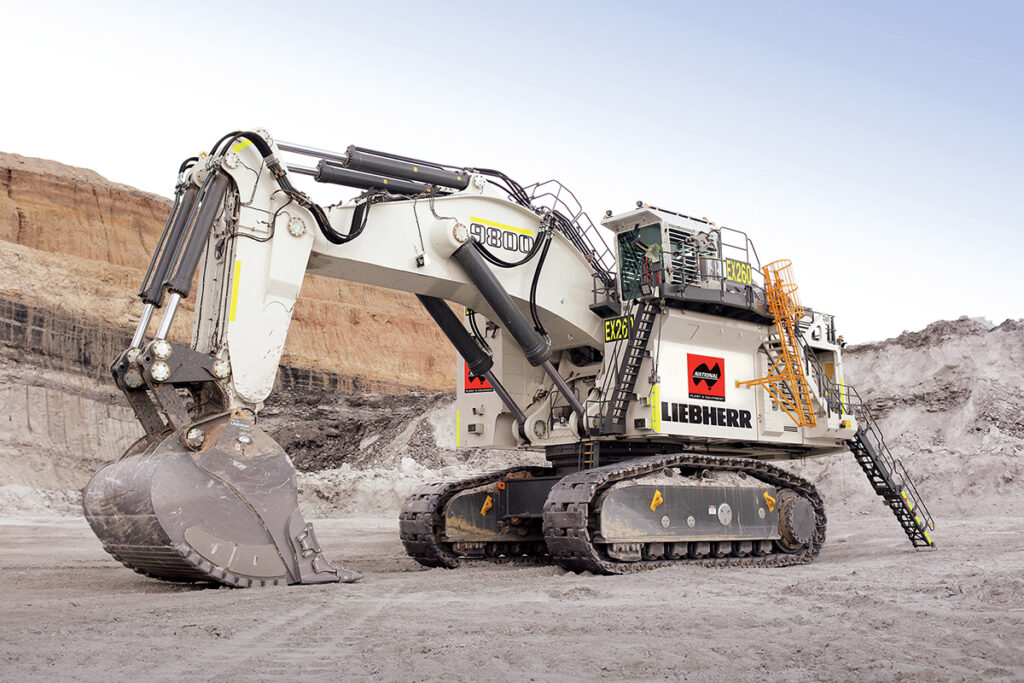
Few understand the logistics involved in heavy haulage, with multi transport modes often required and global logistics management an integral part of the process. Haulage companies regularly have to liaise with government departments including local councils, with relationships, industry knowledge and extensive planning key to success. Police escorts and road closures are often required in order to move some of the largest loads to some of the most remote places and harshest climates in Australia, and indeed the world.
“Forward planning is key to the successful delivery of heavy mining equipment” suggests Ian Scott, General Manager of National Heavy Haulage, part of the National Group.
“Before we even think about transporting equipment, it is important that we survey the surrounding environment and transportation routes proposed before proceeding to the actual haul itself. All relevant parties must be kept informed, which includes the Department of Transport and State or Territory Police.”
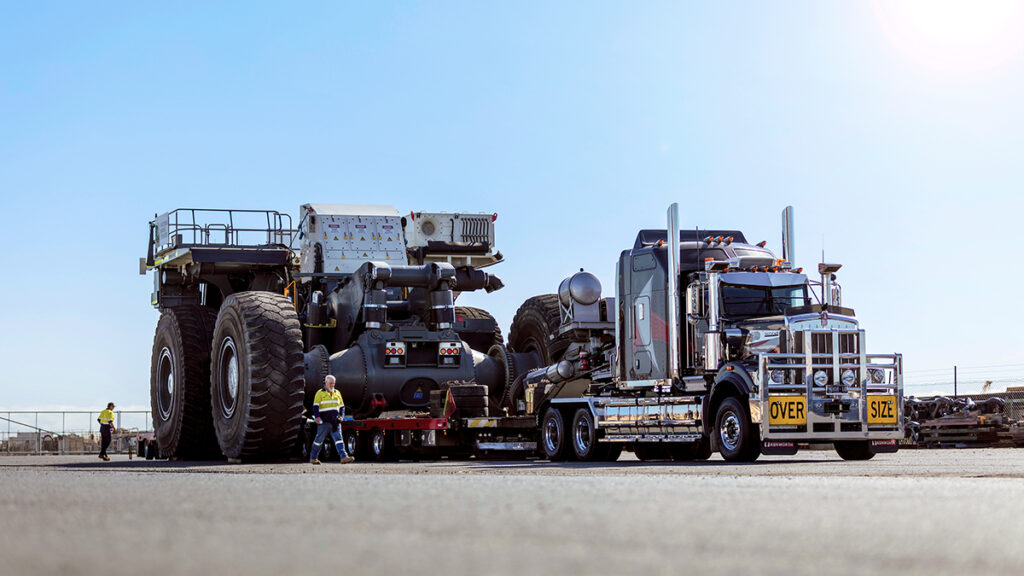
Alongside national heavy haulage, often comes international shipping. Overseas transport poses a whole host of other factors that need to be accounted for and often works hand in hand with domestic heavy haulage when it comes to international transportation.
“International delivery very much operates in a chain structure” suggests Dean Sterling, General Manager of International Global Logistics, part of the National Group.
“Each link in the chain of events relies heavily on the next, in order to ensure adherence to tight delivery schedules and more importantly, safety for all parties involved. Multi-transportation modes are common practice, with equipment often reaching the port by road, rail or sea before it continues its journey to its final destination.”
“Like with national transport of heavy equipment, largo cargo for international transport must clear customs and satisfy security laws, with good relationships with the relevant authorities a must.”
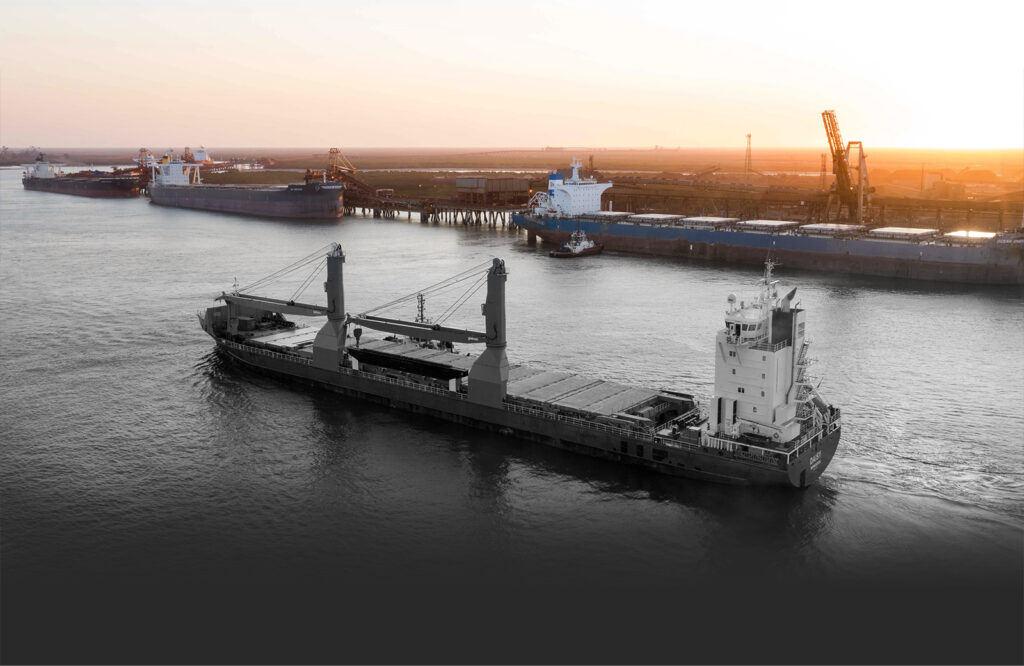
In summary, Mark Ackroyd explains that “mining is a complex industry where the stakes are high and the rewards great. It takes meticulous planning and flawless execution in order to succeed, with the logistics chain only as strong as its weakest link. The future of mining is both exciting and uncertain. The rise of autonomous mining equipment is promising; it will help improve safety and create efficiencies not seen previously. But past and present global events will forever remind us that the future is not always certain and that planning is key to the long term success of any operation.”